Composite Insulators
Composite insulator with Modular Process (Seamless):
Of all the processes associated with the manufacture of insulator housing, the modular process offers the greatest flexibility. Any technically useful creepage distance can be set for a composite solid core or hollow core insulator of a 1iven length. The cylindrical insulator housing is freely extruded from any mold line concentrically onto the rod. Due to the simplicity of the process, special highly ageing-resistant HTVs with a high ATH content can also be used for this purpose. This coordination with the material used for sheds makes sense because, primarily, the shank can typically be damaged by partial discharges. Sheds are manufactured separately in tools that contain multiple mold cavities.
The choice of vulcanized system and the level of rework required essentially determine the level of productivity. The sheds can have different diameters and/or under ribs, and are applied to the cylindrical housing in a fur1her step. The use of under ribs results in a greater creepage distance per shed, which 1ives rise to the following & two application philosophies:
• For a given creepa1e distance, the number of sheds in comparison to a flat profile without under ribs falls and the distance between each shed rises. It must be noted that each shed also results in a protected creepa1e distance for the shank. Therefore, in this cost-optimized variant, if there are fewer sheds, the creepage distance is less protected and there may be a loss of hydrophobicity, assuming that the operating conditions are adequate.
• The insulator length Is limited and a certain creepage distance is required. In these cases, it was possible to successfully use under rib sheds as a technical compromise.

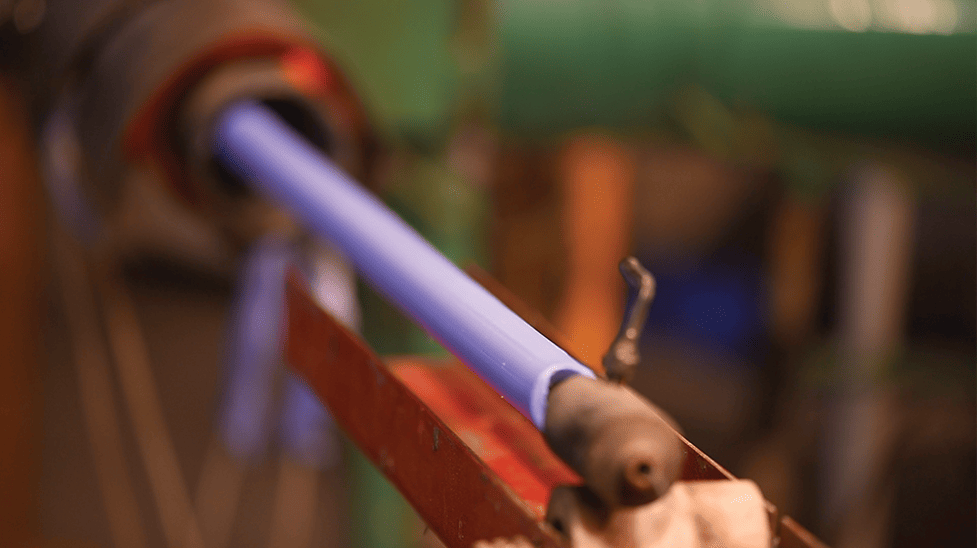
Clamping molds or machines are used to apply the sheds to a rod with extruded silicone rubber housing, it has proven beneficial for the inner diameter of the sheds to be smaller than the outer diameter of the extruded silicone rubber housing. The resulting press fit stabilizes the shed position until the silicone rubber used to achieve an adhesive bond between the sheds and shanks has been fully vulcanized (often known u “silicone adhesive”). To secure the interface between two vulcanized silicone elastomers, the specific property of silicone rubber is used to achieve chemical vulcanization of three physically independent components through the use of an additional silicone elastomer. the “chemistry” for an acetate system (RTVl-) that reacts when acetic add is released. The fine-particle silica (HOK) in silicone rubber plays an important role here: Since not all hydroxyl 1roups of HOK react during vulcanization of the sheds and the shank material, they are available for subsequent reactions. The silicone adhesive (RTVl- or RTV2- system) applied where the shed is positioned or applied liberally over the shank reacts with the HOK and produces an adhesive composite. Bonds are also created without the direct presence of water.
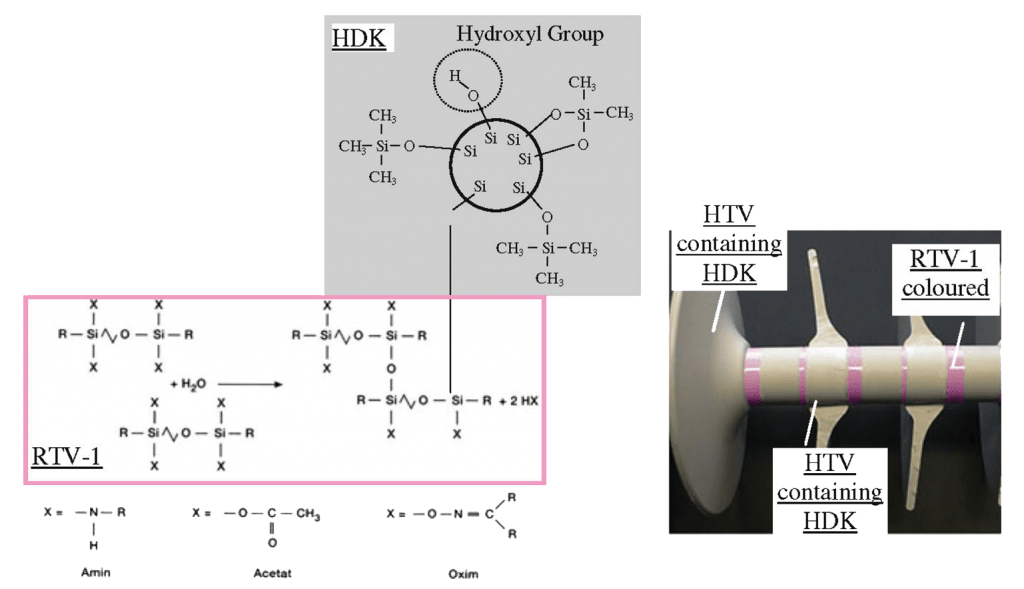